Печатные платы
Системы прямой металлизации
Более 40 лет в процессах сквозной метализации отверстий использовался палладий в качестве катализатора для химического меднения, но за последние 12 лет зарубежье перешло к процессам прямой металлизации, в которых палладий используется для создания проводящего подслоя, не нуждающегося в последующем химическом осаждении меди.
История
Прямая металлизация, по существу, итог борьбы между двумя технологиями металлизации — электрохимической и химической, в которой последняя проиграла. Многие помнят, сколько соблазнов сулили аддитивные процессы производства печатных плат на основе толстослойной химической металлизации. Наблюдались отдельные успехи на этом направлении. Дальше остальных в этом продвинулась фирма Photocircuits, создав промышленную технологию массового производства плат для управляемых снарядов. Но многочисленные попытки дальнейшего распространения этой технологии, в том числе в России (СССР), относящиеся к 70-м годам прошлого столетия, не увенчались успехом. Оно и понятно, процесс химической металлизации до нужных толщин (25 мкм) длится часами (скорость осаждения — 1 …2 мкм/час); в течение всего этого времени нужно поддерживать работоспособность раствора по пяти параметрам: рН, концентрации меди и восстановителя, редокс-потенциалу, температуре, не допустимы даже малейшие градиенты концентраций и температур в объеме ванны. Для компенсации длительности процесса осаждения объем ванн составлял кубометры, чтобы разместить в них необходимое количество плат, соответствующее суточному объему производства. В отличие от этого электрохимическая (гальваническая) металлизация идет с большей скоростью — порядка 30 мкм/ч (при плотности тока 2,5 … 3 А//дм 2).
Чтобы в какой-то мере использовать состоявшиеся наработки, были предложены процессы «среднетолщинной » химической металлизации (порядка 3 мкм), якобы избавляющие производителей от необходимости последующей гальванической затяжки. Почему «якобы »? Потому что химически восстановленная медь — рыхлый осадок, не способный противостоять быстрому окислению. Это создает множество проблем на последующих операциях обработки плат и не гарантирует надежности внутренних межсоединений в МПП.
До недавнего времени в производстве надолго удержалась только всем известная тонкослойная химическая металлизация в сочетании с гальванической затяжкой. Под нее строились технологические линии, создавались химические системы, накопилась значительная база знаний. Что же побуждает теперь отказываться от этого процесса в пользу малоизвестного пока в России процесса прямой металлизации? Что хорошего обещает эта замена?
Сравнение химической и прямой металлизации
Как известно, процесс химической металлизации состоит из двух стадий: активация и химическое восстановление меди на центрах активации. На первой стадии создаются закрепленные на поверхности диэлектрика отдельные вкрапления палладия — катализатора первоначального процесса химического восстановления металла. Поскольку процесс химического меднения — автокаталитический процесс, дальнейшее разрастание металла по поверхности диэлектрика идет без участия палладия. Зоны осаждения смыкаются, за счет чего образуется сплошная проводящая пленка из меди (рис.1).
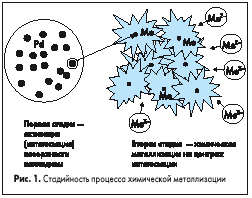
Идея прямой металлизации состоит в том, что на поверхности диэлектрика создается сплошная проводящая пленка без химического восстановления меди. Другими словами, мы имеем возможность исключить процесс химического меднения за счет того, что уже на первой стадии палладий настолько диспергирован по поверхности, что образует сплошную проводящую пленку без последующей стадии химического восстановления меди и без необходимости гальванической затяжки. Поверхностной проводимости этой пленки достаточно, чтобы качественно провести последующую полную электрохимическую металлизацию до стандартных толщин.
Процессы прямой металлизации относятся к так называемым «зеленым » технологиям из-за отсутствия в них комплексообразующих веществ и формальдегидов, хелатов, тяжелых металлов, что уменьшает проблемы, связанные с очисткой сточных вод и делает эти процессы экологически безопасными. И это первое преимущество прямой металлизации.
Второе преимущество ряда процессов прмой металлизации состоит в отсутствии необходимости гальванической затяжки, свойственной процессу химической металлизации. Гальваническая затяжка затрудняет аппаратную реализацию непрерывности процесса в линии химического меднения: после операций химического меднения приходится перезагружать платы на катодные подвески или изначально вести весь процесс на катодных подвесках, в которых нет необходимости на химических операциях.
Третье преимущество прямой металлизации проявляется в обработке отверстий малого диаметра. При химической металлизации, кроме осаждения меди, неизбежно выделяется водород:
Cu2+ +2HCHO +4OH ®Cu + 2HCOO – ++2 H 2 O +H 2 ^
Выделяющийся водород закупоривает отверстия, мешая завершению процесса. Для дегазации отверстий приходится предпринимать специальные меры: наложение ультразвука, вибрацию подвесок, принудительное прокачивание отверстий рабочими растворами, что не всегда удается. В прямой металлизации этот вредный процесс выделения водорода отсутствует.
Наличие формалина и большого количества щелочи делает раствор химической металлизации вязким, с большим поверхностным натяжением, что затрудняет его обмен на стенках отверстий. Из-за этого реакция восстановления металла в узких отверстиях замедляется, неравномерность осаждения сказывается на качестве и устойчивости процесса. Укрывистость поверхности при химической металлизации достигается увеличением продолжительности процесса, а значит, и увеличением толщины покрытия. Учитывая относительную рыхлость химических осадков, это всегда плохо, особенно для многослойных печатных плат. Растворы прямой металлизации имеют меньшую вязкость и поверхностное натяжение. И хотя приемы перемешивания растворов в процессах прямой металлизации используются в той же мере, как и для химической металлизации,прямая металлизация проходит устойчивее химической. И это четвертое преимущество.
Поскольку химическое меднение — процесс автокаталитический, неизбежно металлизируются и вся поверхность фольги наружного слоя, и торцы контактных площадок внутренних слоев. Это приводит к нежелательному расходу реагентов, а для многослойных плат — к наличию непрочного барьерного слоя из химической меди между металлизацией отверстий и торцами внутренних слоев (рис.2).
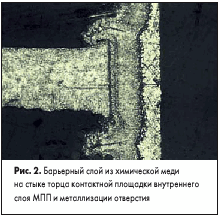
Большая часть отказов межсоединений в МПП сосредоточена именно здесь. В проти воположность этому процессы прямой металлизации организованы так, что проводящая пленка создается только там, где нужно — на диэлектрике.Это пятое преимущество.
Ряд процессов прямой металлизации более устойчив в производстве при неизбежных колебаниях режимов (как теперь выражаются — «имеет широкие операционные окна»). И это не последнее их преимущество.
Переход от химической к прямой металлизации не обязательно связан с приобретением новой линии. Поскольку процесс прямой металлизации имеет меньшее количество операций, традиционные линии химической металлизации с избытком достаточны для организации этого процесса. Необходимо только иметь в виду, что для реализации преимуществ прямой металлизации требуется более тщательная очистка отверстий с созданием развитой поверхности.
Ряд процессов прямой металлизации успешно проводится не только в вертикальных,но и в горизонтальных линиях. Это важно, поскольку в горизонтальных линиях создаются лучшие возможности автоматизации процессов, используются меньшие объемы растворов и промывных вод.
Наконец, использование процессов прямой металлизации сокращает количество операций и, значит, уменьшает время технологического цикла и объем оборудования (табл.1 и 2).
Таблица 1. Сравнение качественных характеристик химической и прямой металлизаций
Параметр |
Химическая металлизация |
Прямая металлизация |
Стадийность процесса |
Активация +химическая металлизация +гальваническая затяжка |
Активация |
Плотность осадка |
Рыхлый |
Плотный |
Наличие барьерного слоя между гальванической металлизацией
отверстия и торцами контактных площадок на внутренних слоях |
Есть |
Нет |
Необходимость гальванической затяжки |
Есть |
Не для всех систем |
Выделение водорода |
Есть |
Нет |
Управления процессом |
По пяти параметрам |
По двум параметрам |
Вязкость раствора |
Вязкий |
Менее вязкий |
Поверхностное натяжение |
54 дин/см |
40 дин/см |
Таблица 2. Стадийность процессов химической и прямой металлизаций
Традиционное химическое меднение |
Палладиевая система System S J Kem |
Графитовая система для вертикальной линии J Graph Immersion Dip Line |
Графитовая система для горизонтальной линии J Graph Horizontal Line |
8 стадий обработки,12 промывок |
5 стадий обработки,7 промывок |
5 стадий,5 промывок |
4 стадии,4 промывки |
1.Очистка поверхностей |
1.Очистка поверхностей |
1.Очистка поверхностей |
1.Очистка поверхностей |
Промывка |
Промывка |
Промывка |
Промывка |
Промывка |
Промывка |
Промывка |
Промывка |
2.Микротравление |
2.Предактиватор |
2.Графит |
2.Графит |
Промывка |
3.Активатор |
3.Активатор |
|
Промывка |
Промывка |
Промывка |
3.Микротравление |
3.Предактиватор |
Промывка |
Сушка |
Промывка |
4.Активатор |
4.Ускоритель |
Сухой бокс |
4.Антиокислитель |
Промывка |
Промывка |
4.Микротравление |
Промывка |
Промывка |
Промывка |
Промывка |
Сушка |
5.Ускоритель |
5.Антиокислитель |
5.Антиокислитель |
|
Промывка |
Промывка |
Промывка |
|
Промывка |
Сушка |
Сушка |
|
6.Химическое меднение |
|
|
|
Промывка |
|
|
|
Промывка |
|
|
|
7.Гальваническая затяжка |
|
|
|
Промывка |
|
|
|
8.Антиокислитель |
|
|
|
Промывка |
|
|
|
Сушка |
|
|
|
Системы прямой металлизации
Как стало понятно, собственно палладиевая система прямой металлизации родилась из процесса активации поверхности диэлектрика для химической металлизации. Основная идея использования палладиевых систем была сформулирована в патенте Радовского (Radovsky) в 1963 году [1 ], по которому был заявлен метод, использующий пленку палладия в полуколлоидальной форме для прямой металлизации сквозных отверстий печатных плат. Изобретение Радовского не нашло тогда применения. Идея использования графито-углеродных систем относится к еще более ранним временам применительно к гальванопластике.
В настоящее время наиболее известны 4 основные системы прямой металлизации [2 ]:
- Коллоидные системы,содержащие палладий.
- Углеродная или графитовая системы.
- Процесс,основанный на осаждении токопроводящих полимеров.
- Другие методы.
1.Палладиевые системы
Палладий-оловянный активатор с гальванической затяжкой
ЕЕ-1 — первая нашедшая промышленное применение система прямой металлизации. Система была заявлена в 1982 году фирмой Photocircuits. В ней использовался активатор палладий-олово с последующей гальванической затяжкой. Ванна затяжки содержала полиоксиэтилен для предотвращения осаждения меди на поверхность фольги, не мешающий осаждению палладия на непроводящие поверхности. Осаждение начиналось от медной фольги и эпитаксиально росло по активированной поверхности отверстия. Покрытие завершалось за 5 –6 мин. Эта затяжка предшествует общему гальваническому осаждению меди до полной толщины. Последующее микротравление удаляет набросы палладия и устраняет гвоздевой эффект на торцах внутренних слоев. Используется специальный очиститель и восстановитель.
Палладиевый/оловянный активатор с блескообразователем
В этом процессе используется палладиевый/оловянный активатор с последующим блескообразователем. Ванна для блескообразования содержит полиоксиэтиленовое соединение для замедления осаждения меди на поверхности фольги, при этом замедление осаждения палладия на непроводящих поверхностях не происходит. Покрытие нарастает на активированной поверхности отверстий. Процесс занимает от 5 до 6 минут. Впоследствии блеск достигается в полном объеме, как при комбинированном позитивном методе, так и при тентинг-процессе в любой гальванической ванне. Микротравление в комбинации с ускорителем удаляет палладий и «шляпки гвоздей » с поверхности торцов внутренних слоев. Используется специальный очиститель-кондиционер.
Оловянно-палладиевый активатор с ванилином
Эта система прямой металлизации была изобретена в Японии в конце 80-х годов. В ней используется оловянно-палладиевый активатор с ванилином, с последующим гальванопокрытием тентинг-методом или комбинированным позитивным способом. Задействован специальный очиститель-кондиционер и карбонатный ускоритель. Все три ключевых раствора — очиститель-кондиционер, активатор и ускоритель — действуют при повышенных температурах. На завершающей стадии в отверстиях получается прочная сероватая проводящая палладиевая пленка. Известно, что очиститель-кондиционер частично разбавляет активатор, притягивая его к непроводящей поверхности. Ванилин выстраивает в цепочку молекулы палладия, ориентируя их вдоль поверхности, за счет чего уменьшается электрическое сопротивление и улучшается адгезия. Небольшая часть палладия и олова остается на медной фольге, для избавления от этого производят слабое подтравливание.
Перевод палладия в сульфид
Crimson-процесс фирмы Shipley использует перевод палладия в сульфид палладия, который должен обладать лучшей проводимостью для последующего гальванического нанесения меди. Усиливающий агент стабилизирует проводящую пленку для того, чтобы она была химически стойкой при последующих операциях фотолитографии. Стабилизатор нейтрализует остатки усиливающего агента, предотвращая загрязнение растворов на последующих стадиях обработки. При селективном микротравлении активатор удаляется с медных поверхностей, чем достигается прочная связь и эпитаксиальный рост металлизации отверстий от торцов контактных площадок внутренних слоев.
Варьирование палладиевых процессов
Технология АВС предложена в Израиле, она сходна с процессом ЕЕ-1. Технология Conductron от LeaRonal сходна с системой прямой металлизации,но с добавлением стадии очистителя-кондиционера и травления стеклотекстолита.
Технология Envision от Enthone-OMI и технология Connect от Atotech довольно сходны, хотя в обеих технологиях используются специфичный очиститель-кондиционер и модифицированный ускоритель.
В технологии Neopact от Atotech используется палладиевый активатор в коллоидном состоянии, не содержащий олова. Последующий процесс POSTDIP удаляет защитную полимерную пленку с палладиевой поверхности, освобождая ее для контакта с растворами. При этом повышается проводимость.
Прямая металлизация System-S от J-KEM International применяет для активации — ключевой стадии обработки — трехметальную коллоидную систему вместо типичной оловянно-палладиевой. Третьим металлом выбран амфотерный металл из III или IV группы таблицы Менделеева. В щелочном растворе постактиватора или интенсификатора (J-KEM) этот металл способен образовывать соединения с Pd и (или)Sn, значительно повышая проводимость в отверстиях (рис.3).
System-S от J-KEM — относительно новая система, разработанная в технологических университетах Швеции и Италии с учетом потребностей современного производства печатных плат. Это обеспечило ей преимущества, отличающие System-S от других систем:
- лучшую селективность осаждения, что особенно важно для МПП;
- возможность металлизации практически любых диэлектриков, в том числе полиимида, полиэфиров, фторопласта;
- равномерное покрытие тонких отверстий (отсутствие эффекта «собачьей кости »);
- возможность металлизации глухих отверстий;
- управляемость процессом в «широких окнах »;
- стабильность растворов;
- высокая проводимость;
- отсутствие необходимости в гальванической затяжке;
- возможность использования в горизонтальных и вертикальных линиях.
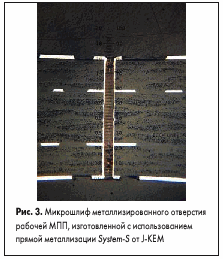
2.Системы на основе графита
Углеродные суспензии
«Black Hole » — вторая по значимости технология прямой металлизации. Запатентована доктором Carl Minten в 1988 году и испытывалась Olin Hunt, который продал их технологию MacDermid в 1991 году. MacDermid значительно усовершенствовал процесс и назвал его «Black Hole II ». Вместо палладиевого активатора используются углеродные суспензии со средней проводимостью. Специальный раствор смачивает непроводящие поверхности и абсорбирует углеродные частицы. После нагревания углеродные частицы выстраиваются в цепь. Для повышения проводимости обработка в углеродных суспензиях выполняется по крайней мере дважды. Остатки углерода должны быть удалены с поверхности медной фольги на стадии микроочистки.
Графит
Используются суспензии графита, обладающего средней проводимостью. Последовательность процесса очень проста и включает в себя немного стадий. Electrochemicals и Eidschun Engineering сделали этот процесс дешевым и компактным.
3.Системы проводящих полимеров
DMS-E — это второе поколение процесса DMS-2 от Blasberg. DMS-1 был похож на EE-1. После микротравления и кондиционирования в растворе перманганата калия в отверстиях образуется покрытие из диоксида марганца, который действует как окислитель в течение последующей реакции синтеза. В каталитической стадии мономер EDT (этилендиокситио-фен) смачивает поверхности диоксидом марганца. В стадии фиксации серной кислоты происходит самопроизвольная окислительная поляризация. На непроводящих поверхностях печатной платы образуется черная проводящая пленка полимера EDT.
Compact CP был предложен фирмой Atotech в 1987 году. По существу, данный метод схож с DMS-E. Но в нем комбинируются стадии фиксации и катализа, используется кислый перманганат, а проводящая пленка состоит из полипиррола.
4.Другие способы
Для полноты списка нужно упомянуть другие возможные варианты металлизации отверстий печатных плат, такие, как Phoenix и EBP от MacDermid, Schlotoposit от Schlotter. В этих технологиях применяются проводящая краска, лазерная возгонка металла в сочетании со сверлением отверстий, вакуумное напыление и магнетронная металлизация. Но они не получили столь широкого распространения как вышеперечисленные.
Заключение
Прямая металлизация — прямой путь к избавлению от капризных процессов химической металлизации с сокращением объемов прямых и капитальных затрат.
Она намного облегчает решение экологических проблем, устойчивее в управлении, обеспечивает хорошую адгезию металлизации ко всем известным диэлектрикам и ряд систем прямой металлизации не требует гальванической затяжки.
Палладиевые системы прямой металлизации дают более устойчивые и качественные результаты и особенно необходимы для МПП. рафитовые системы дешевле, но их использование не может выходить за рамки двусторонних печатных плат.
Использование готовых фирменных концентратов, приготовленных в профессиональных условиях фирм-производителей, гарантирует качественный результат прямой металлизации в предписанных режимах использования.
Литература
- Clyde F.Coombs.Printed Circuits Handbooks.Fifth Edition.McGraw-Hill.2002.
- Степанов В.Прямая металлизация:да или нет?//Компоненты и технологии.2002.№ 6.
Jurgan Lundquist, J-Kem International AB, Аркадий Медведев, проф. МАИ, Валентина Салтыкова
|